Tyre construction
Up to 30 different kinds of rubber, fillers and other substances are used in a tyre’s rubber. They are mixed in blenders to create a black, gummy compound. The tyre is then built from the inside out and then cured to form its final shape. The cooled rubber is cut into strips that will form the basic structure of the tyre itself. At the milling stage, other elements of the tyre are prepared, some of which are then coated in another type of rubber. The textile elements, steel belts, beads, ply, tread, and other components are then assembled on a tyre-building machine. The tyre is the vulcanised with hot moulds in a curing press, compressing all of the parts together and giving its final shape, including its tread pattern and manufacturer’s sidewall markings.
The process is reconstructed in the following video-animation.
Courtesy of U.S. Tire Manufacturers Association (USTMA) and ETRMA.
Rolling resistance
The elasticity of tyres, mainly made of rubber, provides the necessary functions to ensure comfort and safety, but there are trade-offs, the main being absorption of energy opposing to the vehicle movement, called “rolling resistance. The lowest rolling resistance is only obtained with no tyres, as in the wheels of trains and trams.
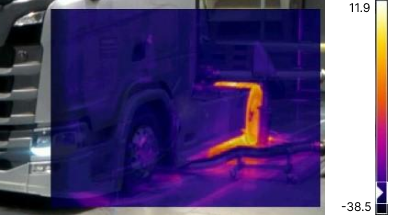
An infrared image of a test of rolling resistance on a truck tractor: the heat generated by the hysteresis is clearly visible (Hyttinen et al. Effect of Ambient and Tyre Temperature on Truck Tyre Rolling Resistance. Int.J Automot. Technol. (2022)).
As a tyre flexes when it rotates, friction between molecules causes energy to be converted into heat: this is known as hysteresis loss. Such loss accounts for the bulk of the rolling resistance (over 90%), the remaining being due to adhesion and sliding between the road and the tyre.
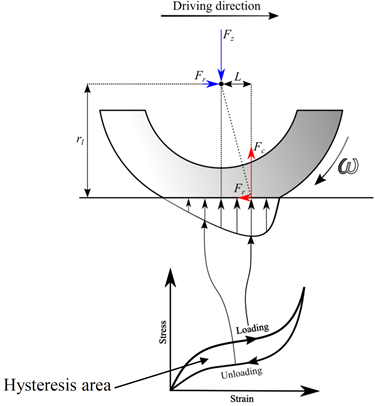
The forces involved in the deformation of a rolling tyre. (Source: J. Hyttinen, Modelling and experimental testing of truck tyre rolling resistance),
Rolling resistance is highly responsible of vehicles energy consumption: for example it accounts for about 40% of a diesel truck energy consumption, but with the increased efficiency coming from more aerodynamic cabin design, from autonomous trucks and from electrification, it could relatively increase to 60% or more. In any electric vehicle, moreover, lower rolling resistance would result in more energy recovered during the recuperation (regenerative braking), an additional further gain in range and contribution to the decrease of battery size!
As a battery electric vehicles is about three times more efficient than a similar internal combustion engine (ICE) vehicle, a poorly rated tyre in terms of rolling resistance has three times the negative impact: e.g. changing from an A-rated tyre to a C-rated can reduce range by over 8%. Rolling resistance of tyres, consequently is getting increasing attention, as involving:
- For the general consumer, liters of difference in gasoline consumption or tens of kilometers of range for every refuelling/recharge
- For the business, an important and relatively increasing voice of cost of road transport
- For the environment and all of us, a relevant cause of energy use and additional pollution.
It must be clarified that rolling resistance is finally influenced by different factors:
- Tyre design: for this, EPREL can help you chose the most efficient tyres
- Road design: e.g. a very noisy asphalt involves higher energy use (noise production as well involves energy use)
- Weather conditions: a wet surface or, worse, a snowy one, considerably increases the resistance to advancing of the vehicle
- Vehicle design: improving aerodynamics and decreasing weight helps reduce energy use (i.e. a SUV consumes far more energy than a station wagon with the same motor and comparable internal space).
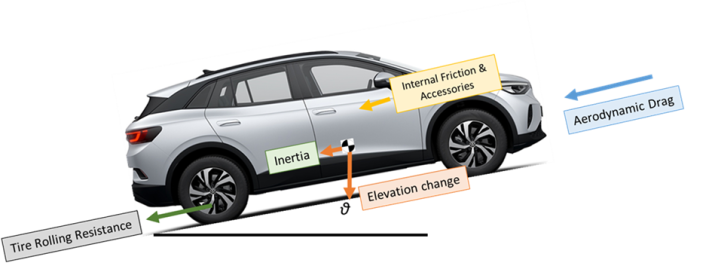
Main forces opposing vehicle motion (Courtesy of Goodyear)
The rolling resistance is rated in the label in 5 classes. Rolling Resistance Coefficient” (RRC) limits for every class are indicated in a table (from Annex I or the Tyre Labelling Regulation).
Wet grip
‘Wet grip’ is the tyre’s ability to stick to the road in wet conditions. Ensuring safety is a crucial aspect: adherence and control of vehicles on a wet, slippery road is a frequent necessity, at all latitudes. A slick tyre has the best possible adherence on a dry road, but makes the vehicle increasingly uncontrollable with water on the road, for increasing speeds, leading to the so-called "aquaplaning", i.e. a situation of complete lack of maintaining the direction of the vehicle. Tyre tread design is specifically intended to ensure water evacuation, but also the tread depth and the compounds are relevant.
Safety on a wet road is rated in the label in terms of "wet grip". The test to grade the tyre is performed by launching a vehicle on a wet surface: the shorter the distance for completely stopping the vehicle when the brake pedal is fully pushed, the best the class in the tyre label.
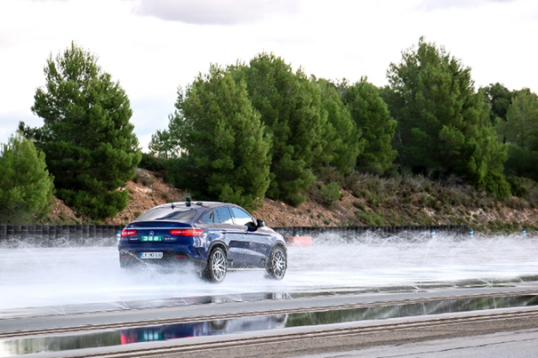
Testing wet grip, i.e. distance covered to stop the vehicle on wet asphalt (Courtesy of IDIADA).
The wet grip is rated in the label in 5 classes, focusing on one aspect of wet grip, i.e. the wet braking performance. You may assume that each class is equivalent to about 3-4 meters, making a huge difference in some situations. Wet grip index limits for every class are indicated in a table (from Annex I or the Tyre Labelling Regulation). Each wet grip class involves a few extra meters necessary to stop the vehicle on a wet surface.
Wet grip may degrade with the aging of the tyre but especially with wear (tread depth diminution): for this reason a new minimal requirement has been set in the legislation for wet grip in half-worn tyres.
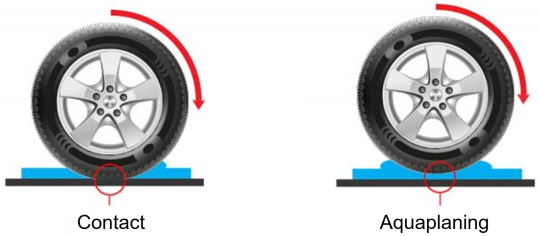
Aquaplaning: when it occurs (Courtesy of TireAmerica)
Wear (abrasion and mileage)
Abrasion is the unavoidable loss of rubber material during rolling and sliding contact of the tyre with the road, which results in the peeling-off of rubber debris (particulate matter). Most of debris is encrusted to with other particles from asphalt: mostly deposited onto the road surface, road runoff plays a crucial role in spreading these "microplastics". These particles interact with water and air, triggering degradation and concomitant release of components such as tens of different organic and inorganic additives: the tyre particles and the leachates derived from them during their degradation in the environment can cause biological responses in aquatic and terrestrial biota.
Mileage, or, rather, kilometrage, is an indicator of the durability of tyres in terms of total distance run until the tread depth reaches the minimum allowed by safety legislation (i.e. 1,6 mm in passenger cars). A short mileage results in additional waste to be treated (for the whole tyre carcass) and in a higher lifecycle cost for an earlier tyre replacement (to which a cost for mounting, balancing and vehicle unavailability must be added).
According to a consumer survey of 2019, mileage, with rolling resistance, are the most relevant parameters in customers purchase choice for replacement tyres, after wet grip, as both involve relevant money savings.
Mileage and abrasion indicators will be added to the label, as soon as suitable testing methods will be available (work in progress), as foreseen by the tyre labelling Regulation.
Rolling noise
All tyres produce some noise but snow tyres and off-road car one’s sound louder, as well as the run-flat, because of the stiffer sidewalls.
External rolling noise measured level is expressed in A-weighted decibels -dB(A)- that is the relative loudness of sound as perceived by the human ear and it is indicated on the label with a pictogram symbol of a loudspeaker. Noise classes are 'A', 'B' or 'C’ , however the C class is almost not populated and the B class is the most crowded (i.e. most of tyres are in the B class, you can see the situation by querying EPREL). The class is not directly determined by the emitted noise level but depends on the limits according to the UN ECE Regulation 117 (a table with the limits is not simple, as depending on the year of approval of the tyre). The set limits are different depending on the tyre class (i.e., passenger car, van, or bus/truck). For passenger cars, the wider the section the higher the noise but also the limit set. An allowance of 1dB(A) is provided to winter and to XL tyres. Similarly for bus/truck tyres, different limits are set for traction and for other tyres, for normal and for snow tyres. The noise limits became more stringent since January 2023.
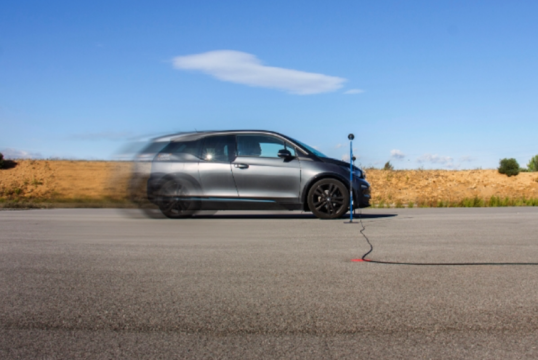
Testing of external rolling noise (Courtesy of IDIADA).
For testing the “external rolling noise”, a sound level meter measures noise levels: a microphone is positioned at the height of the ears of an average tall person and the vehicles passes by 8 times at speeds around 80 km/h for car and van tyres and around 70 km/h for bus/truck tyres.
Competing properties
Rolling resistance, noise, wet grip and wear are competing properties, e.g.:
- Hysteresis is negative for rolling resistance, but positive for grip and traction/handling;
- Lower rolling resistance may be negative for mileage or wear.
For example, rolling resistance may be reduced by diminishing the tread depth, but this, in turn, may result in less mileage, i.e. less kilometers run by the tyre before it reaches the minimum depth allowed by safety norms to ensure sufficient grip on wet roads (i.e. 1,6 mm).
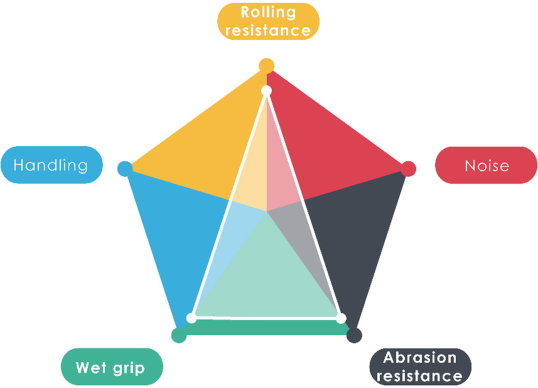
The multidimensional complexity of competing tyres properties (Source: Sustainable mobility - Elsevier - Javier Araujo-Morera et al.)
For this reason, the tyre label is aiming at providing a balanced information for the purchase choice. Wet grip is the second parameter rated in tyre labels, so that the customer is guided in choosing the tyres that excel both in rolling resistance and in safety. A mileage class should be added, once a suitable tyre testing method has been agreed.
Efficient driving for long lasting tyres
Regularly check tyre pressures: low pressure increases fuel consumption, affects braking performance and vehicle responsiveness and causes irregular and premature wear. Optimal tyre pressure is prescribed by the vehicle manufacturer: usually it is indicated in a sticker inside the fuel tank door or in the driver’s door frame (as well as in the vehicle manual). For many vehicles a different pressure is prescribed if at full load or when carrying the driver only.
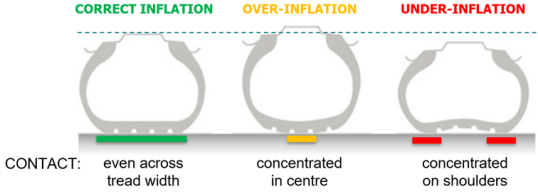
Comparing different inflation levels.
A few use recommendations to ensure a longer life of tyres :
- Internal tyre pressure increases with the temperature: measure the pressure after the vehicle has been not in movement for hours, as it increases after a few kilometres of travel (because of hysteresis). Recall that in winter air pressure decreases, thus you have to inflate more your tyres;
- The highest the pressure, within the prescribed limits, the lowest the hysteresis and thus the kilometres run using the same energy;
- Avoid harsh acceleration and deceleration, to reduce both both fuel consumption and tyre wear;
- Extra weight increases not only fuel consumption but also tyre wear; regularly clear out non-essential items from your car.
- Check for signs of uneven wear on the tyres, especially along the edges of the front tyres. Uneven wear could indicate a tracking or camber problem that could increase fuel consumption and cause your tyres to wear more quickly.
- Camber is the term for how far the wheel tilts outward or how far it leans inward toward the vehicle: a wrong camber angle causes a ring of wear towards the inside or outside edge of the tyre, so check your tyres in this respect;
- Tracking, or wheel alignment, is a mechanical adjustment of the vehicle suspension system to ensure that wheels turn in the correct position. A constant pulling to one side on the straight may be a symptom of incorrect alignment: wheel misalignment causes irregular wear and premature replacement need;
- If you periodically rotate tyres, check the tyre uneven wear first, or you would lose the information about which wheel or axis needs to be checked;
- A vibration of the steering may be a symptom of incorrect equilibration of the tyres.
Annexes (tables)
The rolling resistance is rated in the label in 5 classes. The following table indicates the “Rolling Resistance Coefficient” (RRC) limits for every class (as indicated in Annex I or the Tyre Labelling Regulation).
Fuel efficiency | C1 (passengers) | C2 (vans) | C3 (buses/trucks) |
---|---|---|---|
Class | RRC in N/kN | RRC in N/kN | RRC in N/kN |
A | RRC ≤ 6,5 | RRC ≤ 5,5 | RRC ≤ 4,0 |
B | 6,6 ≤ RRC ≤ 7,7 | 5,6 ≤ RRC ≤ 6,7 | 4,1 ≤ RRC ≤ 5,0 |
C | 7,8 ≤ RRC ≤ 9,0 | 6,8 ≤ RRC ≤ 8,0 | 5,1 ≤ RRC ≤ 6,0 |
D | 9,1 ≤ RRC ≤ 10,5 | 8,1 ≤ RRC ≤ 9,0 | 6,1 ≤ RRC ≤ 7,0 |
E | RRC ≥ 10,6 | RRC ≥ 9,1 | RRC ≥ 7,1 |
Back to rolling resistance section
The wet grip is rated in the label in 5 classes. The following table indicates the “wet grip index” limits for every class (as indicated in Annex I or the Tyre Labelling Regulation).
Wet grip | C1 tyres | C2 tyres | C3 tyres |
---|---|---|---|
Class | wet grip index | wet grip index | wet grip index |
A | 1,55 ≤ G | 1,40 ≤ G | 1,25 ≤ G |
B | 1,40 ≤ G ≤ 1,54 | 1,25 ≤ G ≤ 1,39 | 1,10 ≤ G ≤ 1,24 |
C | 1,25 ≤ G ≤ 1,39 | 1,10 ≤ G ≤ 1,24 | 0,95 ≤ G ≤ 1,09 |
D | 1,10 ≤ G ≤ 1,24 | 0,95 ≤ G ≤ 1,09 | 0,80 ≤ G ≤ 0,94 |
E | G ≤ 1,09 | G ≤ 0,94 | G ≤ 0,79 |